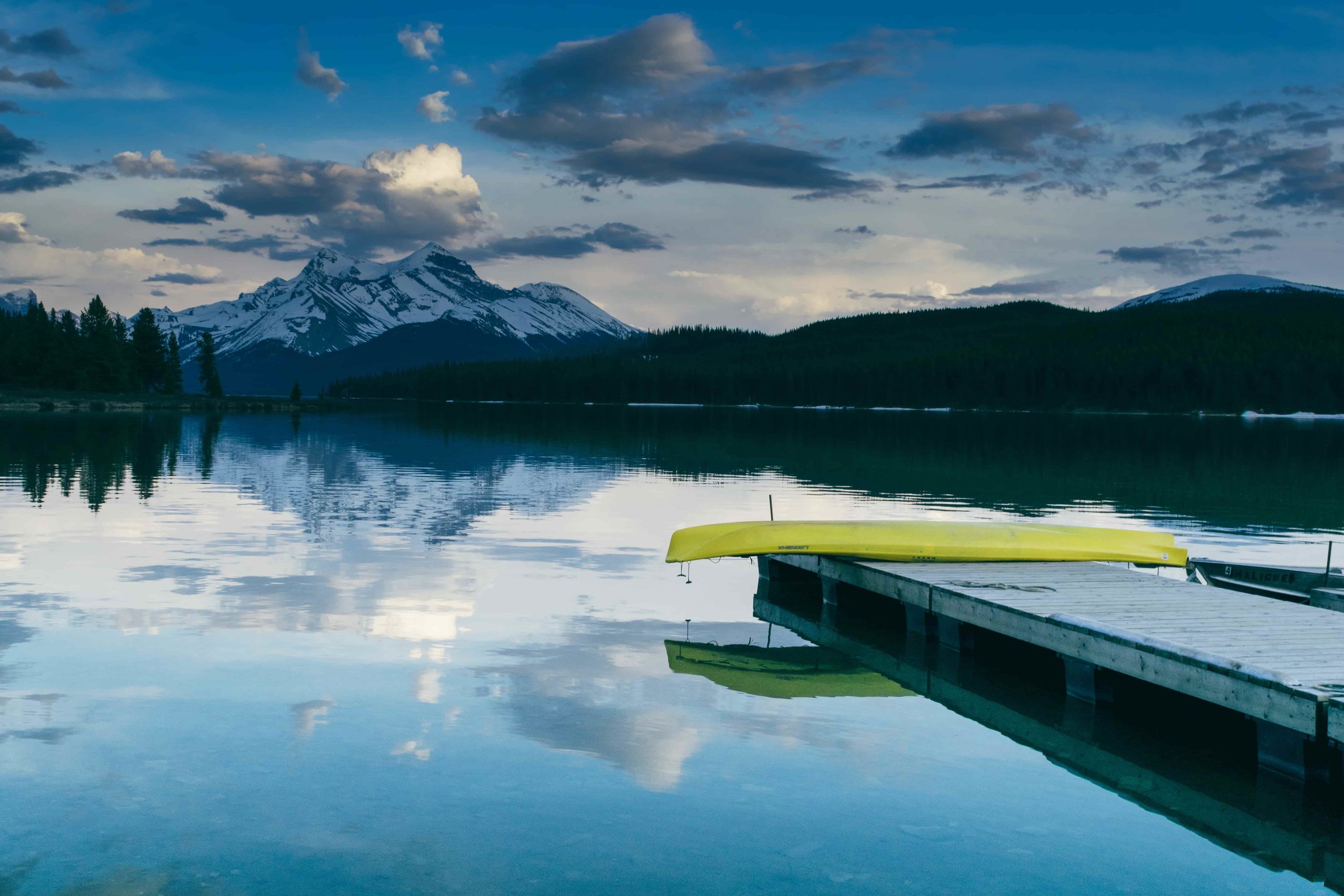
THE SUPPLY CHAIN BLOG
5 Supply Chain Trends for 2021
This past year has created many new challenges for everyone, causing consumers and companies to adapt. We expect some of the supply chain changes to be temporary but that many of them will have a lasting impact on the supply chain industry going forward. Below, we discuss some of the trends that we expect to see in 2021.
This past year has created many new challenges for everyone, causing consumers and companies to adapt. We expect some of the supply chain changes to be temporary but that many of them will have a lasting impact on the supply chain industry going forward. Below, we discuss some of the trends that we expect to see in 2021.
Fulfillment and Logistics as a Competitive Tool
Every year we continue to see consumer behavior change, and in no year has that change happened as rapidly as in 2020. People want to get quality goods for a reasonable price and quickly. Unorganized supply chains will become increasingly exposed as companies will have to choose between bad service levels or unsustainable costs to meet customer demand. The most obvious example of this trend is Amazon's move to achieve next-day or same-day shipping. As stated above, consumer expectations for service continue to rise. This means businesses that have systems in place to forecast well, stock optimal levels of inventory and fulfill efficiently have a significant advantage over those that do not.
Focusing on E-Commerce, Service Levels and Omnichannel Development
The shift from brick and mortar retail to e-commerce has been growing every year, and COVID-19 only expedited that growth even more. It's no surprise that consumer’s extreme shift to e-commerce seen in 2020 will have a lasting effect on the way people do business moving forward. In addition to the e-commerce shift, service levels are also becoming a higher focus as consumers are going to choose the quickest and most reliable option. To keep up with these shifts, companies are going to have to continue to focus on developing their omnichannel strategy. This means using support systems to create an interconnected network of stores, warehouses and 3PLs, providing the flexibility to fulfill both large wholesale purchases and small e-commerce orders. Companies can then leverage this interconnectivity within the network to optimize fulfillment strategy on an order level basis.
Shifting E-Commerce to a 3PL
Another industry trend we expect to see is a significant shift for e-commerce distribution towards third-party logistics companies (3PLs). The e-commerce industry, in comparison to brick and mortar stores, presents a complexity that is hard to tackle for smaller companies. 3PLs provide an option that will allow companies to set up much quicker than if they opened their own warehouse and allow them to avoid significant fixed costs, have access to an already established network and get specialized processes based on their needs.
Making Procurement a Focus
COVID-19 complications and global trade friction with China mixed with consumer’s increasing expectations for better service have signaled to the supply chain world that now may be the time to focus on procurement. By moving suppliers closer to home (near-shoring) and prioritizing the procurement process to make lead time and flexibility priorities, companies can improve their fulfillment times and overall supply chain. Developing a regional supply chain offers the better potential for mutually beneficial relationships and improves both time and proximity to market. This confidence in relationship management and product could challenge the prior approach of low-cost country sourcing.
Freight Normalization – A New Baselinne
COVID-19 has caused overwhelming increases to volume causing capacities to be tested and costs and rejection rates to skyrocket. As the freight companies profit on these higher rates, it can be expected that they will reinvest into capital expenditures, such as more trucks, increasing capacity to meet market demand and normalizing from the economic shifts of 2020.
We wish everyone a safe and healthy 2021.
Outsourced vs In-House Transportation: A Guide
All companies at some point have to make a decision on what aspect of a business to keep in-house, and what should be outsourced. Transportation is such a critical part of a supply chain that many companies leave it to specialist third party logistics (3PL), but depending on the type of company and the trajectory of the business, insourcing could be a valuable investment.
All companies at some point have to make a decision on what aspect of a business to keep in-house, and what should be outsourced. Transportation is such a critical part of a supply chain that many companies leave it to specialist third party logistics (3PL), but depending on the type of company and the trajectory of the business, insourcing could be a valuable investment.
The three main options for transportation are:
1. Contract Carriage: An agreement between an established carrier and another party for transportation. This is the most popular option as it is the most well-known and the most flexible. The upside to this option is that there is no transportation management other than scheduling pickups and deliveries for products as they are ready to ship. The downside is that the transportation is at the mercy of big trucking companies and if there are emergency shipments it’s not always possible to schedule last-minute transportation.
2. Private Fleet: Owning tractors and trailers and employing drivers to run transportation operations. A private fleet enables a company to have complete ownership of the transportation network. The benefit to this is that there is total control over the operation, but this comes with the burden of managing a separate entity that is likely not the company’s specialty. It requires capital to invest in trucks and trailers, as well as hiring and retaining drivers and adhering to regulations for these truck drivers. Very consistent demand and shipments would be required to justify this option.
3. Dedicated Fleet: Assigning a group of tractors, trailers, and drivers exclusively to fulfill transportation needs. This option is essentially a private fleet but is managed by experienced companies, so is somewhere in the middle of insourcing and outsourcing. This is a desirable option often because companies do not want to deal with the intricacies of owning a private fleet, but they want the flexibility and service levels that come with owning it. Dedicated fleets are usually run through 3PLs.
Declining Business: 3 Key Ways to Save in Warehousing Costs
Three ways to help cut warehousing costs to prolong your positive cash flow.
Here are 3 key ways to help cut warehousing costs to prolong your positive cash flow:
1: Data-Driven Forecasting
Completely accurate forecasting is hard to achieve, but frequent, data-driven forecasts with informed strategic adjustments are the key to determine how much product nee on-hand inventory is needed. Being able to plan for While this seems basic, there are other areas where accurate forecast can help save money in the future. For example, if you are using a 3PL and can say that your inventory levels will drop x amount each year, your footprint in their warehouse should drop as well allowing the 3PL to fill that space with other clients thus saving you money.
2: Inventory Analysis
In a business that’s losing demand, there’s a good chance that the are certain items that maintain the demand while most others are being phased out. It is very important to keep track of the demand for each individual SKU in the warehouse. An ideal situation would be to set up all the slow-moving SKUs as direct shipments from the manufacturer while keeping only the high moving SKUs in the warehouse. While the shipment costs directly from manufacturer to customer will likely be higher, the savings from not keeping the inventory in stock will outweigh the increased shipping costs. Another option to look into would be to separate slow-moving SKUs in one smaller and centralized warehouse. You can keep the inventory levels low allowing you to lower the footprint. Staffing needs will also be reduced since the handling of these SKUs is much less than in the faster moving warehouse.
3: Inventory and Staffing Management
Proper inventory management is important for all businesses, but it is especially important in declining ones. Start by looking into any trends that might be developing in the orders. It is important to think of outside the box methods for optimizing your warehouse strategy. Instead of looking at storing the SKUs by size or product line, look to see if there are certain items that are usually part of the same order. Group these items close together in your warehouse to save on the handling costs. Instead of storing 1 small SKU per bin, store 3 in each by adding in dividers to the bins. There is also a greater need for cross training of the staff in a slower moving warehouse. There will be much more down time and you cannot afford to have employees not being productive. There will be a slight learning curve at the beginning when the employees are learning the other job functions of the warehouse, so productivity might go down. This is fine as the returns once the cross training is complete will be much greater than the lost production early on.