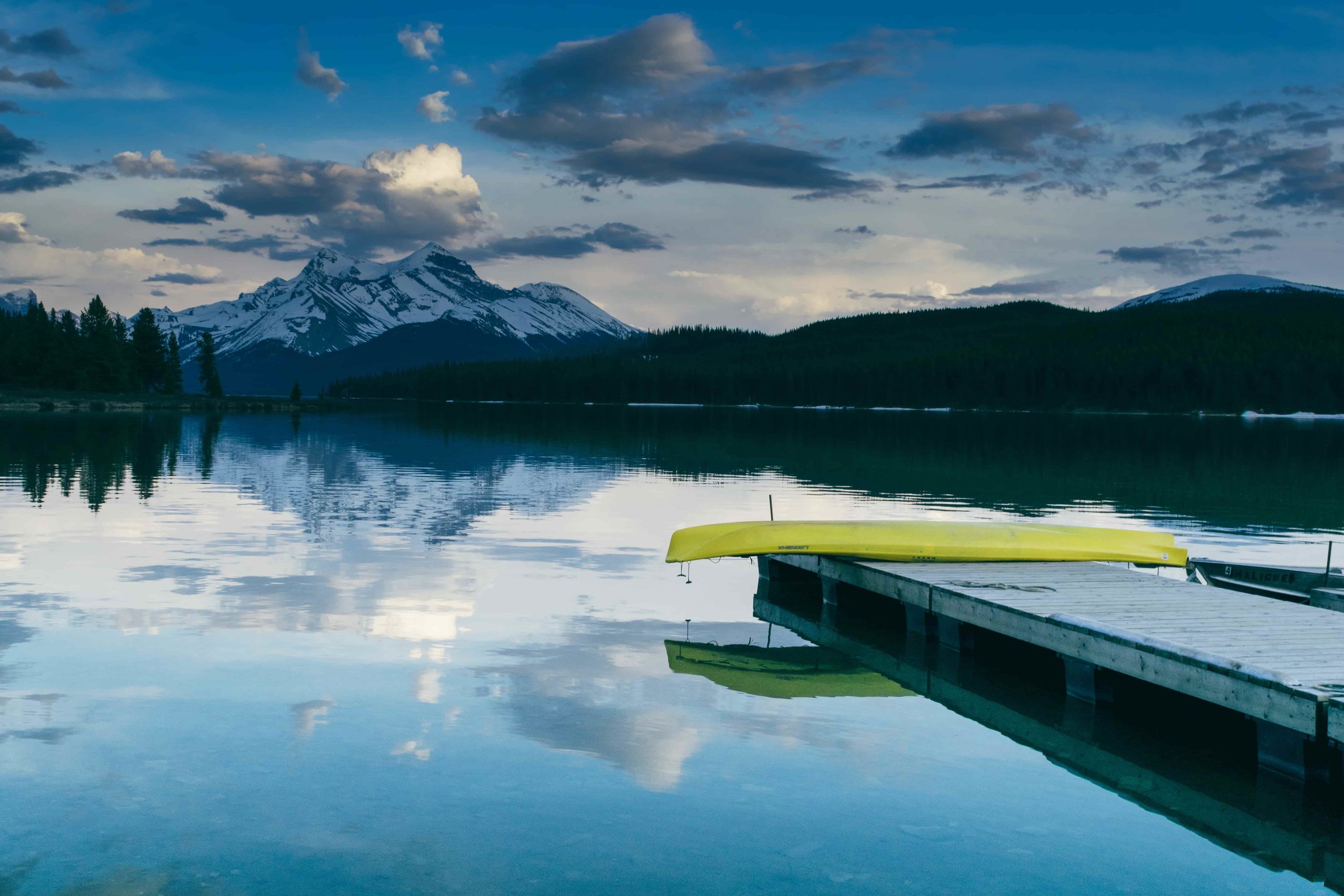
THE SUPPLY CHAIN BLOG
Warehouse Optimization: Maximizing Space Utilization and Reducing Costs
In the world of supply chain management, warehouses play a crucial role in storing and distributing goods efficiently. However, many companies struggle with limited space and rising operational costs, which can hinder productivity and profitability. The key to overcoming these challenges lies in warehouse optimization. By maximizing space utilization and reducing costs, businesses can unlock significant benefits and gain a competitive edge in the market. In this post, we will explore practical strategies and actionable tips to optimize your warehouse operations and get the most out of your warehouse or distribution center.
In the world of supply chain management, warehouses play a crucial role in storing and distributing goods efficiently. However, many companies struggle with limited space and rising operational costs, which can hinder productivity and profitability. The key to overcoming these challenges lies in warehouse optimization. By maximizing space utilization and reducing costs, businesses can unlock significant benefits and gain a competitive edge in the market. In this post, we will explore practical strategies and actionable tips to optimize your warehouse operations and get the most out of your warehouse or distribution center.
Conduct a Comprehensive Warehouse Layout Analysis: A crucial step in warehouse optimization is analyzing the current layout to identify inefficiencies and areas for improvement. Consider factors such as storage density, product flow, accessibility, and safety. By critically evaluating your warehouse's layout, you can identify opportunities to reorganize storage areas, implement better aisle configurations, and utilize vertical space effectively.
Embrace Technology and Automation: Incorporating technology and automation solutions can revolutionize your warehouse operations. Implementing the right Warehouse Management System (WMS) can streamline inventory control, order fulfillment, improve overall accuracy, and enable further improvements. Additionally, technologies like barcode scanning, RFID tagging, and automated systems can enhance picking and packing processes, reducing human errors, and saving valuable time.
Prioritize Inventory Management and Sales and Operations Planning (S&OP): It is very important to look at supply chain planning from a holistic, end to end, point of view. This will help the overall business on a strategic level and positively impact the warehouse operation by having better inventory management. Successful S&OP and inventory management is crucial for space optimization and cost reduction. By understanding your inventory levels, turnover rates, and demand patterns strategies can be implemented that minimize excess stock, reduce carrying costs, and maximize available space. Furthermore, adopting an ABC analysis methodology can help prioritize items based on their value and optimize storage allocation accordingly.
Implement Lean Principles: Applying Lean principles to warehouse operations can lead to significant improvements in space utilization and cost reduction. Techniques such as 5S (Sort, Set in Order, Shine, Standardize, Sustain) can improve the efficiency at workstations by eliminating waste and creating an organized and efficient workspace. Lean methodologies also promote employee involvement, creating a culture of continuous improvement.
Optimize Slotting and Picking Strategies: Effective slotting and picking strategies can minimize travel time, reduce labor costs, and enhance overall warehouse productivity. Analyze your SKU velocity and order patterns to strategically place fast-moving items closer to shipping areas, reducing the time taken to pick and pack high-demand products. Regularly review and adjust your slotting strategies to align with changing demand and business requirements.
Foster Collaboration with Suppliers: Collaborating closely with suppliers can help optimize warehouse operations and reduce costs. Explore vendor-managed inventory (VMI) programs which allow suppliers to monitor and replenish stock levels directly. This reduces lead times, minimizes stockouts, and frees up your warehouse space. Additionally, explore opportunities to change that way that vendors ship product to help expedite the receiving and put away processes. Potential changes include packaging, labels, and cross-docking practices to reduce handling.
Warehouse optimization is a critical aspect of supply chain management that can yield significant benefits for businesses. By maximizing space utilization, implementing efficient processes, and leveraging technology, companies can reduce costs, improve productivity, and enhance customer satisfaction. Remember, optimizing your warehouse is an ongoing process that requires continuous monitoring, analysis, and adaptation to evolving market dynamics. By adopting the strategies discussed in this blog post, you can take a proactive approach towards warehouse optimization, unlocking its full potential and positioning your business for success in the competitive market landscape.
Warehouse Scanning Technology: Additional Options to Elevate Your Warehouse Operation
Warehouse operations are continuously evolving to meet the growing demands for efficiency, accuracy, and speed in order fulfillment. While handheld RF scanners have been a staple in warehouse environments for data capture, advancements in technology have introduced alternatives that offer enhanced capabilities and improved productivity. In this post, we will explore alternatives that are redefining warehouse operations, surpassing the limitations of handheld RF scanners and opening doors to new levels of efficiency and automation.
Warehouse operations are continuously evolving to meet the growing demands for efficiency, accuracy, and speed in order fulfillment. While handheld RF scanners have been a staple in warehouse environments for data capture, advancements in technology have introduced alternatives that offer enhanced capabilities and improved productivity. In this post, we will explore alternatives that are redefining warehouse operations, surpassing the limitations of handheld RF scanners and opening doors to new levels of efficiency and automation.
Wearable Technology - Empowering Hands-Free Productivity: Wearable technology, such as ring scanners or wrist-mounted devices, is emerging as a popular alternative to handheld RF scanners. These compact devices provide hands-free scanning capabilities, allowing warehouse personnel to move freely while scanning items. With wearable scanners, workers have improved agility, enabling them to perform tasks quickly and efficiently. The convenience and ease-of-use of wearable technology streamline order picking processes, resulting in enhanced productivity and reduced fatigue.
Voice Picking Systems - Harnessing the Power of Voice Recognition: Voice picking systems leverage voice recognition technology to guide warehouse personnel through picking activities. Workers wear a headset and receive verbal instructions on which items to pick and where to find them. By responding with voice commands, workers confirm their actions, eliminating the need for manual data entry or scanning. Voice picking systems improve accuracy, enhance worker safety, and eliminate the need for handheld devices altogether. This technology allows for seamless integration with warehouse management systems, further optimizing operational efficiency.
Mobile Computers - The Power of Data and Functionality in One Device: Mobile computers, also known as rugged tablets or handheld computers, offer a versatile solution for warehouse operations. These devices combine the functionality of a scanner and a portable computer in a single device. Equipped with built-in barcode scanners or capable of connecting to external scanners, mobile computers provide a larger screen for displaying information and enable real-time communication with warehouse management systems. They offer additional functionalities beyond scanning, such as inventory management or order tracking, empowering workers with comprehensive data and tools at their fingertips.
Vision Systems - Advancements in Visual Recognition Technology: Vision systems leverage cameras and image recognition technology to capture and process data in warehouse operations. These systems can automatically scan and decode barcodes or labels, eliminating the need for manual scanning. By integrating vision systems with conveyor belts or automated sorting processes, items can be identified and tracked accurately without human intervention. Vision systems offer rapid and reliable data capture, improving efficiency and throughput in the warehouse while reducing reliance on handheld scanners.
RFID Technology - Enabling Real-Time Inventory Visibility: RFID (Radio Frequency Identification) technology has gained prominence in warehouse operations, offering a highly efficient alternative to handheld RF scanners. RFID tags are attached to items, pallets, or containers, and RFID readers or antennas capture the data wirelessly. Unlike traditional barcode scanning, RFID technology does not require line-of-sight scanning and can read multiple items simultaneously. This enables real-time inventory visibility, automates tracking processes, and reduces manual data entry, resulting in improved accuracy and streamlined operations.
As the demand for speed, accuracy, and efficiency in warehouse operations continues to grow, alternatives to handheld RF scanners are revolutionizing the industry. Wearable technology, voice picking systems, mobile computers, vision systems, and RFID technology offer advanced capabilities that surpass the limitations of traditional handheld scanners. By leveraging these alternatives, warehouses can enhance productivity, improve worker safety, achieve real-time inventory visibility, and streamline operational processes. Embracing these advancements empowers warehouses to stay ahead of the competition, meet customer expectations, and unlock new levels of efficiency and automation in their operations.
Order Picking in the Warehouse: Choosing the Right Strategy
Order picking is one of the most important processes in a warehouse or distribution center, making up the majority of operating costs and directly impacting service levels. Selecting and implementing the right picking strategy will ensure accurate on-time deliveries and cost-effective labor. In this article, we will review some different order picking strategies and how they can improve an operation.
Order picking is one of the most important processes in a warehouse or distribution center, making up the majority of operating costs and directly impacting service levels. Selecting and implementing the right picking strategy will ensure accurate on-time deliveries and cost-effective labor. In this article, we will review some different order picking strategies and how they can improve an operation.
Single Order Picking
One of the most common picking methods is single order picking. Just as it sounds, this method requires one order to be picked at a time, from start to finish, by a single operator. This method is easy to learn, does not require advanced technology, and is less prone to errors due to its simplicity. Single order picking is best suited for smaller warehouses or where entire pallets are picked. For larger and more complex operations, single order picking becomes inefficient due to the high amount of travel required throughout the warehouse.
Batch Picking
Opposite to single order picking, batch picking groups multiple orders together that have the same SKUs, which are later sorted by an operator before being shipped. The main advantage batch picking has over single order picking is the ability to pick multiple orders in a single trip, which improves operator productivity. Due to the increased complexity of batch picking, a warehouse management system (WMS) and order management system (OMS) are required to properly route and track orders throughout the warehouse.
Cluster Picking
For cluster picking, multiple orders are picked, from start to finish, by a single operator. This method is different than batch picking in that each order is sorted as it is picked. This is accomplished with the help of a cart containing individual totes for the operator to place SKUs in as they are picked. Cluster picking does not require a warehouse management system (WMS) and works best for smaller orders and smaller warehouses. This can create significant improvement from single order picking since the operator’s total distance traveled is reduced.
Zone Picking
With zone picking, the warehouse is split into individual zones that an operator will pick from. Operators will pick all the SKUs for an order in their zone and then send it to pack or the next zone if it is incomplete. This method can be used independently or in conjunction with the above-mentioned methods. This is a valuable option for high volume warehouses that struggle with operator congestion in aisleways.
Wave Picking
Wave picking can be utilized independently or in congruence with the above-mentioned methods. Wave picking groups orders together and releases them to operators in batches or “waves”. Orders can be grouped together based on a variety of different factors, such as shipping schedules, shift changes, product characteristics, etc. Wave picking is best suited for operations that are using batch or zone picking, already have a warehouse management system (WMS) and order management system (OMS) in place, and are looking to fully optimize their picking strategy.
Choosing the right order picking strategy is a great start to optimizing a warehouse operation. The best strategy will vary based on company size, inventory size, number of orders, SKUs per order and technological capabilities. At Establish, we combine a fact-based approach with state-of-the-art technology including warehouse simulations and data analytics to determine the optimal picking strategy for organizations.