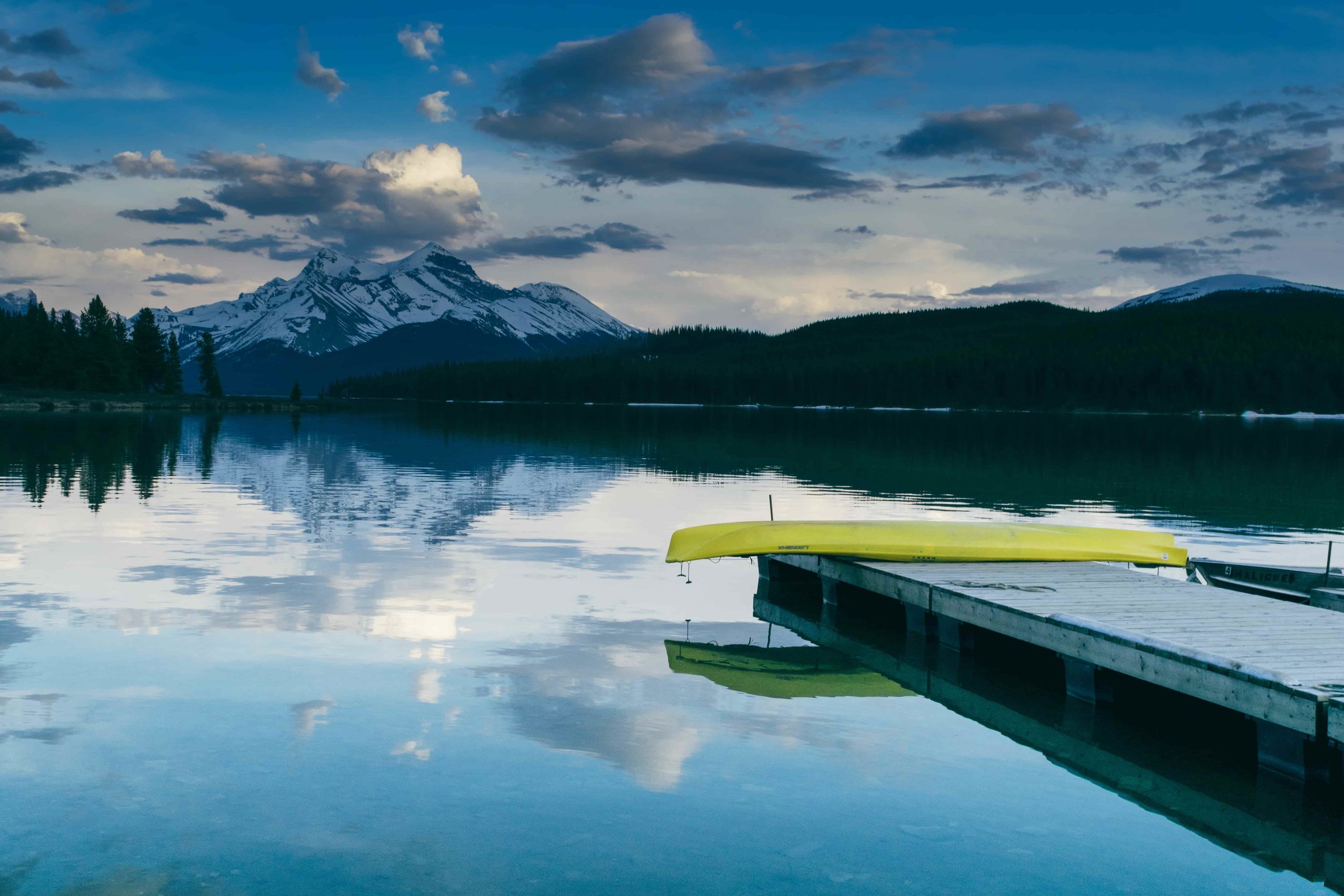
THE SUPPLY CHAIN BLOG
Lighting the Way: Profoto Selects Barrett Distribution Centers as Its U.S. 3PL Partner
Read about how we helped our client, Profoto, the global leader in light-shaping technology for imaging professionals, select and go live with Barrett Distribution Centers as its third-party logistics (3PL) provider in the United States.
FRANKLIN, Mass., July 14, 2025 /PRNewswire/ -- Profoto, the global leader in light-shaping technology for imaging professionals, has selected Barrett Distribution Centers as its third-party logistics (3PL) provider in the United States. Operations are now live at one of Barrett's facilities in Somerset, N.J.
As premium brands face increased pressure to deliver faster and more reliably, Profoto's partnership with Barrett reflects the growing need for logistics providers that can move quickly without sacrificing quality.
"We ran a competitive RFP process, led by our global partner, Establish Inc., and Barrett quickly rose to the top," said Daniella Stolpe, business operations and IT manager at Profoto. "Their location near our key customer in New York, strong systems and analytics, and attention to detail really impressed us. Most of all, it was the people. Barrett was responsive, thorough and truly invested in building a long-term partnership."
Barrett's solution includes receiving ocean and airfreight shipments, cycle-count inventory management, secure pick-and-pack services for fragile goods, returns processing, parcel and LTL transportation management and supply procurement.
"Profoto faced a sudden non-renewal from its previous 3PL, creating an urgent need for a smooth transition," said Sally Caputo, head of 3PL services at Establish. "Barrett delivered an on-time go-live with API integration, real-time visibility and improved shipping rates. We've placed other clients with them and continue to see the high-level service we expect."
To meet the tight timeline, Barrett's engineering and IT teams designed a flexible warehouse layout and completed a fast-tracked integration aligned with Profoto's ERP migration.
"Profoto needed a partner who could move fast and scale with their growth," said Scott WIlkins, vice president of customer solutions at Barrett. "Our team delivered on time and collaborated seamlessly. We're proud to support their U.S. expansion."
The partnership highlights how Barrett meets high-performance brands' complex supply chain needs through personalized solutions, real-time visibility and scalable operations.
About Profoto
Founded in 1968 and headquartered in Sweden, Profoto is the world's leading manufacturer of photography lighting equipment, trusted by the best photographers in the industry, especially in fashion. With presence in nearly 50 countries and subsidiaries in New York, Tokyo, Hamburg, Paris, London and Scandinavia, Profoto sets the standard for innovation and quality. Combining a legacy of photographic excellence with a dynamic, disciplined culture, Profoto delivers premium lighting solutions that shape the future of professional image creation.
About Barrett Distribution Centers
Since 1941, Barrett has provided customized third-party logistics (3PL), direct-to-consumer (DTC) eCommerce fulfillment, omnichannel distribution, managed transportation solutions and retail compliance for clients across all industries, with a focus on apparel & footwear, health & beauty, consumer packaged goods (CPG) and education. Barrett continues to be a leading 3rd party logistics provider in North America, known for superior execution, customer engagement and direct access to senior leadership decision makers. As a member of Inc's fastest growing companies list 15+ times, Barrett is big enough to do the job and still small enough to deeply care about your business. Brands interested in a new 3PL partnership may contact Barrett directly here.
About Establish Inc.
Establish is a supply chain consulting firm offering specialized services in the optimization of the supply chain. With over 50 years of experience and thousands of projects under their belts, Establish has been trusted by some of the largest and best-known corporations in North America and Europe as well as smaller companies. Establish's lasting success is attributed to their team of the sharpest mathematicians and analysts; armed with the state-of-the-art tools. The delivery of both quantitative analytics and strategic insights makes Establish uniquely qualified to service their clients most pressing supply chain needs. Establish approaches each engagement ensuring recommendations are actionable and sustainable, even leading the implementation of new initiatives through steady state.
How to Ensure a Successful 3PL Implementation
In our previous post, we talked about the importance of defining operational goals and requirements and the need for a thorough partner evaluation and selection. While choosing the right partner is important, the integration and go live process is critical to ensure success. In this blogpost, we will focus on the implementation, which we have broken out into 3 steps, Mapping Integration Points for Systems and Data, Transition Management and Go Live, and Ongoing Management and Continuous Improvement.
Third-Party Logistics (3PL) refers to the practice of outsourcing logistics services to a specialized third-party provider. These services can include warehousing, transportation, inventory management, and freight forwarding. By partnering with a 3PL provider, companies can offload the complexities of logistics, allowing them to focus on their core competencies.
Over the past few decades, the 3PL industry has evolved significantly, offering a wide array of logistics services to businesses across various sectors. Specific to warehousing, operating your own warehouse can be expensive and challenging so many companies decide to leave it to a 3PL provider to conduct these services. Integrating warehouse operations with a 3PL provider offers several advantages for supply chain management, like efficiency improvements, cost savings, flexible labor, scalability, access to specialized expertise, and enhanced customer service. To achieve these improvements, it is imperative that the right partner is selected.
When using a 3PL, the process of selecting and implementing your partner is pivotal but can be a daunting task for businesses. It is essential to have a focused internal or external group driving the selection and integration process. In situations where internal resources are limited or time is constrained, leveraging external expertise can be an optimal path forward. At Establish, we follow a detailed 5 step approach when selecting and integrating a new 3PL provider. Read more about our 3PL consulting services here.
Defining Operational Goals and Requirements: Understand your business objectives and organizational needs. What are you aiming to achieve through 3PL integration?
Partner Selection and Evaluation: Choosing the right 3PL partner is critical. What are the deciding criteria? (Cost, experience, culture?)
Mapping Integration Points for Systems and Data: Seamlessly align your existing systems with the 3PL provider’s infrastructure. Integration points matter.
Transition Management + Go-Live: Execute the transition smoothly. Minimize disruptions during the critical go-live phase.
Ongoing Management + Continuous Improvement: Sustaining success requires initiative-taking management and continuous refinement.
In another blogpost (How to Choose the Right 3PL Partner — Establish Inc.), we talked about the importance of defining operational goals and requirements (step 1) and the need for thorough partner selection and evaluation (step 2). While choosing the right partner is important, the integration and go live process is critical to ensure success. In this blogpost, we will put the last three steps in the spotlight.
Step 3: Mapping Integration Points for Systems and Data
After the 3PL partner selection has been finalized and contract is awarded, it is time to begin the implementation process. One aspect of the transition is designing the system integration. In the collaborative design process, organizations work together to establish seamless connections between their systems. Having the support of third-party resources here helps to keep the project focus, bring in best practices, align business needs between you and the 3PL rather than completely redesigning what is in place, and maintain an efficient integration timeline by managing internal resources effectively. Here is how the system integration typically unfolds:
Designing Data Flows: Teams map out how data moves between different systems. This involves identifying data sources, transformation points, and destinations. Considerations include real-time data exchange, batch processing, and data synchronization. Usually a decision between an EDI, API or more manual integration has to be taken.
Operational Procedures: Collaborators define operational procedures for handling data. This includes data validation, error handling, and exception management. Standardizing procedures ensure consistency and reliability.
Workflow Hand-Offs: Workflow hand-offs occur when one system completes its task and passes relevant data to the next system. Clear documentation and communication are essential to avoid bottlenecks or data loss during hand-offs.
Reporting Integrations: Reporting systems need access to relevant data. Integrations ensure that reporting tools can pull data from various sources. Customized reports, dashboards, and analytics enhance decision-making.
Tailoring to Existing Infrastructure: Organizations adapt integrations to fit their existing technology stack. This involves assessing compatibility, security, and scalability. Legacy systems may require additional connectors or middleware for seamless integration.
By collaboratively addressing these aspects, organizations create robust end-to-end connections that enhance efficiency and drive business success.
Step 4: Transition Management
While system integration is a key milestone in the 3PL integration process, it is important to plan and manage the operational and physical transition with the new partner. To ensure a smooth transition, it is essential to focus on the following areas:
Phased Approach: For larger implementations (multiple sites, business units, or sales channels), considering the benefits of a phased rollout is key. By breaking down the implementation into manageable phases, organizations reduce the risk of large-scale disruptions. For example, for multi-site implementations, every warehouse, partner, or region can have a specific and different go-live-date. Each region becomes a testing ground, allowing adjustments before full-scale deployment. Moreover, phased rollouts provide valuable insights. Organizations learn from early adopters, refine processes, and adapt to regional nuances. Additionally, concentrating on one region at a time ensures efficient resource allocation, and it prevents strain on personnel, infrastructure, and support systems.
Communication and Training: Another important pilar is to establish a plan for communication, training, and testing. Transparent communication with stakeholders is crucial. Inform employees, customers, and partners about the upcoming changes, timelines, and expected impacts in adherence to contractual agreements and operational considerations. Next, it is important to provide comprehensive training to the affected teams. Address their concerns and ensure they feel confident using new systems and offer ongoing support during the transition. From a system and operations perspective, a best practice is to run existing and new systems in parallel, just like exiting partners and entering partners. This minimizes disruptions and allows for gradual adjustments.
Exit Strategy: If there are existing 3PL partner(s) that are losing business, effectively managing the transition away from them can be challenging, but there are strategies to keep them engaged during this critical phase. First and foremost, timely and clear communication is essential. Regular touchpoints and checkpoints should be maintained throughout the entire process. Aligning expectations—both legally and operationally—is highly important. Providing well-defined instructions and thorough documentation facilitates a professional transition. Additionally, keeping a close eye on costs and systems ensures a smooth exit. Given the complexity of this task, it’s often advisable to conduct on-site visits to manage expectations and gain a comprehensive overview of current stated operations.
Be Proactive: When navigating the complexities of a 3PL integration and transition, it is important to be as proactive as possible. Best practices consist of appointing change champions within each region or group – they advocate and promote adoption, address resistance, and encourage positive attitudes. This establishes a feedback loop to capture user experiences and identify pain points. Proactive management involves addressing issues promptly, so it is important to set up the right fora to hear these voices. Setting up a new warehouse comes with challenges and glitches, so it is important to anticipate them and proactively address bottlenecks, technical glitches, and unforeseen obstacles – ensuring the continuous improvement journey to start from the beginning.
Step 5: Ongoing Management and Continuous Optimization
The journey doesn’t end with the go-live event; it extends into the post-implementation period. First, it is key to explain the need for continuous optimization after the initial launch. This involves ongoing assessment, optimization, and a commitment to continuous improvement. An industry best practice is making use of an issue tracker meeting to keep track of open items that need follow up. After go-live, a lot of additional ideas and change requests will come up to help better the operation and add to the scope; it is important to capture and prioritize these correctly.
Once at a steady state, it is also important to discuss governance models, track KPIs and monitor performance. These KPIs will often be defined in the Service Level Agreement (SLA) and summarize the performance of outbound operations, inbound operations, and inventory accuracy. Taking the time to audit the 3PL invoices and ensure their accuracy is also paramount. It provides a sense check that correct rates are being billed as well as accurate operational volumes being billed. Occasionally, there could be systematic errors in the billing function which could be overlooked.
In the end, it is the 3PL’s job to deliver an effective solution for your business, but you can help to facilitate a successful integration and promote continuous improvement by utilizing a consulting partner, like Establish, who will ensure you take the correct steps and set up an effective post go-live structure.
In this blogpost, we have explored the critical steps necessary for a seamless 3PL integration. By partnering with a consulting company like Establish, you can strategically align your operational goals and requirements, ensuring a successful launch and ongoing optimization. Remember, successful 3PL integration isn’t just about technology—it’s about people, processes, and collaboration. With the right approach, you will unlock efficiency gains, cost savings, and improved customer satisfaction. Read more about our 3PL consulting services here.
How to Choose the Right 3PL Partner
Integrating warehouse operations with a 3PL provider offers several advantages for supply chain management, like efficiency improvements, cost savings, flexible labor, scalability, access to specialized expertise, and enhanced customer service. To achieve these improvements, it is imperative that the right partner is selected and the implementation is successful. At Establish, we follow a detailed 5 step approach when selecting and integrating a new 3PL provider. In this post, we will dive into the first 2 steps to and discuss some of the key considerations for selecting the right 3PL partner.
Third-Party Logistics (3PL) refers to the practice of outsourcing logistics services to a specialized third-party provider. These services can include warehousing, transportation, inventory management, and freight forwarding. By partnering with a 3PL provider, companies can offload the complexities of logistics, allowing them to focus on their core competencies.
Over the past few decades, the 3PL industry has evolved significantly, offering a wide array of logistics services to businesses across various sectors. Specific to warehousing, operating your own warehouse can be expensive and challenging so many companies decide to leave it to a 3PL provider to conduct these services. Integrating warehouse operations with a 3PL provider offers several advantages for supply chain management, like efficiency improvements, cost savings, flexible labor, scalability, access to specialized expertise, and enhanced customer service. To achieve these improvements, it is imperative that the right partner is selected.
When using a 3PL, the process of selecting and implementing your partner is pivotal but can be a daunting task for businesses. It is essential to have a focused internal or external group driving the selection and integration process. In situations where internal resources are limited or time is constrained, leveraging external expertise can be an optimal path forward. At Establish, we follow a detailed 5 step approach when selecting and integrating a new 3PL provider.
Defining Operational Goals and Requirements: Understand your business objectives and organizational needs. What are you aiming to achieve through 3PL integration?
Partner Selection and Evaluation: Choosing the right 3PL partner is critical. What are the deciding criteria? (Cost, experience, culture?)
Mapping Integration Points for Systems and Data: Seamlessly align your existing systems with the 3PL provider’s infrastructure. Integration points matter.
Transition Management + Go-Live: Execute the transition smoothly. Minimize disruptions during the critical go-live phase.
Ongoing Management + Continuous Improvement: Sustaining success requires initiative-taking management and continuous refinement.
Read more about our 3PL consulting services here. In this post, we will dive into the first 2 steps to and discuss some of the key considerations for selecting the right 3PL partner. For more details on steps 3 through 5, see our other post How to Ensure Successful 3PL Implementation — Establish Inc..
Defining Operational Goals and Requirements
1. Define Goals:
Why it matters: Clear goals help you choose a 3PL partner that aligns with your business needs, whether it’s cost reduction, faster delivery, or better customer service. Goals also provide benchmarks to measure success and allow the 3PL to tailor services to your requirements. This ensures efficient resource allocation and helps both parties focus on critical areas, making the partnership more effective.
Key Actions: Conduct a thorough assessment of your logistics needs, including current challenges, future growth plans, and specific requirements like warehousing, transportation, or technology integration. Set clear, measurable goals (e.g., reduce shipping costs by 10%, improve delivery times by 20%, expand into new markets within six months). Involve key stakeholders from various departments (e.g., procurement, operations, finance) in the goal-setting process to ensure goals are comprehensive and aligned with the overall business strategy.
2. Data Collection and Analysis:
Why it matters: Data underpins informed decision-making and storytelling. Accurate supply chain, inventory, and operational data help forecast volumes and depict your operation’s current and future state. Capturing forecasted changes in volumes, order profiles, and shipping lanes is crucial for 3PL service. Network studies and shipment data analysis can identify the optimal location for your operation, aiding the 3PL search process.
Key Actions: Gather data on inbound and outbound shipments and order profiles, SKU (Stock Keeping Unit) diversity, inventory levels, lead times, and seasonal fluctuations and apply forecasts. Analyze historical performance metrics to understand trends and pain points. Capture pictures and videos to give additional levels of insight into operations.
3. RFP (Request for Proposal) Development:
Why it matters: An effective RFP sets the stage for successful collaboration with 3PL providers. It outlines your expectations, service requirements, and evaluation criteria. A good mix of qualitative descriptions (explain processes, service levels and requirements) with quantitative measures (forecast volumes, seasonality, order profiles, etc.) should be included in this document. Including storage, product, and shipment example photos or videos provides great visual references for the 3PLs as well.
Key Actions: Craft a detailed RFP that covers service expectations like service levels, technology requirements, reporting, and forecasted volumes to be handled. Be clear about your goals and desired outcomes. Having this document gives you a tool to communicate with potential 3PL partners in a structured, data-driven, and unbiassed way.
Partner Selection & Evaluation
1. 3PL Identification:
Why it matters: Choosing the right 3PL partner significantly impacts your supply chain efficiency so it is important to cast a wide net of potential partners to be a part of the RFP process. By casting a wide net, it allows for better rate and capabilities comparison. In addition, 3PLs have their specific expertise, geographical footprint, vacancy, and historical reputation that impact the decision of their participation in the RFP process.
Key Actions: Research and identify 3PLs based on their capabilities, industry experience, vacancy, and geographic coverage. Consider factors like warehouse locations, transportation networks, and scalability.
2. RFP Management:
Why it matters: Efficient RFP management streamlines selection, ensures timely provider responses, and facilitates fair comparisons. Understanding and negotiating 3PL rate structures is crucial for apples-to-apples comparisons. Given the strategic importance of a 3PL search, effective time management and strict deadlines are essential to maintain momentum.
Key Actions: Communicate promptly with potential partners. Establish proposal review calls and walk through each bid together- asking questions, understanding rates and services, and pinpointing gaps in the proposal. Consider the 3PLs’ responsiveness, alignment with your requirements, and value-added services as part of the evaluation criteria.
3. Strategy Alignment:
Why it matters: A strategic approach aligns 3PL services with your overall supply chain strategy. It ensures long-term success and flexibility with your future partner. It is common for business leaders to sit together with 3PL leadership and share their current and future vision on operations and collaborations. Conducting site visits to see 3PL operations can help support final decision making as well as create a forum to discuss the strategic goals of both parties. The right partner is one that works for the present, but also for the future.
Key Actions: Define your logistics strategy. Consider factors like cost optimization, risk management, and customer service. Evaluate how each 3PL aligns with these goals.
4. Final Selection
Why it matters: The choice of a 3PL provider affects operational efficiency, customer satisfaction, and costs. Their performance impacts order fulfillment, inventory management, and overall supply chain. As an extension of your brand, their service quality directly influences customer experience. While cost is important, it shouldn’t compromise service quality or technology.
Key Actions: Evaluate proposals thoroughly by considering cost, service quality, technology capabilities, and cultural fit. Scrutinize pricing structures and additional fees. Assess the 3PL’s reputation and service quality, and ensure their values and communication align with yours. Verify they have robust technology and reporting systems.
5. Contract Negotiation:
Why it matters: Contract negotiation is crucial because it establishes the framework for the partnership between your company and the chosen 3PL provider. It sets clear expectations, defines roles and responsibilities, and outlines the terms under which services will be delivered. A well-negotiated contract helps prevent misunderstandings, reduces risks, and ensures alignment between both parties.
Key Actions: Negotiate contract terms to protect both parties. Engage in open discussions with the 3PL to agree on terms related to pricing, volumes, service levels, performance metrics, and any specific requirements unique to your business. The contract should safeguard the interests of both your company and the 3PL partner. Address issues such as liability, termination clauses, dispute resolution, and confidentiality.
Having the right 3PL partner can help facilitate growth, improve customer service, and lead to cost savings so it is critical to take the right steps when selecting your partner. If this process seems daunting, consider partnering with a consulting firm like Establish, to guide you through this intricate process. The right consultant partner can offer expert knowledge of the 3PL market and an unbiased evaluation when making a decision. They also can manage the timeline and deliverables efficiently and ensure a structured, data-driven approach and can support additional analyses such as center of gravity and network optimization. Overall, a consulting partner enhances and guides you to an optimal 3PL partner selection which in return, can result in a successful long-term partnership. Read more about our 3PL consulting services here.
A Guide to Warehouse Automation for Every Warehouse
The evolution of technology has been marked by the emergence of technologies that were once considered impossible. The first televisions and computers were bulky, expensive, and limited in their capabilities. However, they paved the way for the development of more advanced devices such as smartphones and tablets. These devices are not only more affordable but also more accessible to a wider audience, enabling them to benefit from the features that were once exclusive to the privileged few. The automation landscape has undergone a similar transformation in recent years. The traditional approach of relying on large, robust, and rather expensive solutions has given way to a more modular, scalable, and affordable approach. This shift has enabled smaller companies to leverage the many advantages of automation that were once only available to larger companies. In this blogpost, we will focus on the advantages of automation, introduce the main technologies, and introduce some operational and budgetary considerations, before jumping into some specific examples.
The evolution of technology has been marked by the emergence of technologies that were once considered impossible. The first televisions and computers were bulky, expensive, and limited in their capabilities. However, they paved the way for the development of more advanced devices such as smartphones and tablets. These devices are not only more affordable but also more accessible to a wider audience, enabling them to benefit from the features that were once exclusive to the privileged few. The automation landscape has undergone a similar transformation in recent years. The traditional approach of relying on large, robust, and rather expensive solutions has given way to a more modular, scalable, and affordable approach. This shift has enabled smaller companies to leverage the many advantages of automation that were once only available to larger companies. In this blogpost, we will focus on the advantages of automation, introduce the main technologies, and introduce some operational and budgetary considerations, before jumping into some specific examples.
Advantages
The rise of automation has revolutionized the way warehouses operate. By leveraging technology, warehouses can now process more orders in less time, optimize their use of space, labor, and equipment, and reduce their reliance on manual labor. This has led to increased revenue, reduced costs, and improved efficiency. In this blogpost, we will explore the benefits of automation in more detail and how it can help warehouses achieve their goals.
Increased warehouse throughput: Automation can help warehouses process more orders in less time, which can lead to increased revenue and customer satisfaction.
Better resource utilization: Automation can help warehouses optimize their use of space, labor, and equipment, which can lead to reduced costs and increased efficiency.
Reduced labor and operational costs: Automation can help warehouses reduce their reliance on manual labor, which can lead to reduced costs and increased efficiency.
Real-time visibility into workflows: Automation can help warehouses track inventory and orders in real-time, which can lead to better decision-making and improved customer service .
Ability to forecast with greater accuracy: Automation can help warehouses predict demand and optimize inventory levels, which can lead to reduced costs and increased efficiency.
In conclusion, automation has transformed the warehouse landscape by enabling warehouses to operate more efficiently and effectively. By embracing automation, warehouses can stay ahead of the competition and achieve their goals.
Main Technologies
Another purpose of this blogpost is to have a deeper look at warehouse automation technologies that can increase efficiency and reduce labor costs. Across different industries and clients, the following technologies would be recommended:
Autonomous Mobile Robots (AMRs): AMRs are a type of robot that can navigate through a warehouse without human intervention. They are equipped with sensors and cameras that allow them to detect obstacles and avoid collisions. AMRs are highly customizable and can help warehouses automate the movement of inventory from one end of the warehouse to another, which can lead to increased efficiency and reduced labor costs.
Automated Storage and Retrieval Systems (AS/RS): AS/RS are a type of warehouse automation technology that can help automate the storage and retrieval of inventory, leading to increased efficiency and reduced labor costs. They are designed to store and retrieve inventory or products automatically, replacing large areas of shelving to save floor space, improve safety, and increase overall productivity. These systems can be designed to work with bins of smaller goods or full pallets and can work with people or integrate with other automated systems.
Automated Guided Vehicles (AGVs): AGVs are another type of mobile robots, equipped with sensors and cameras, that can help warehouses automate the movement of inventory within the warehouse, which can lead to increased efficiency and reduced labor costs.
Warehouse Management Systems (WMS): WMS is software that can help warehouses manage and control daily operations, from the moment goods and materials enter a distribution or fulfillment center until the moment they leave. It offers real-time inventory visibility, picking and packing processes, resource utilization, analytics, and more 1. By automating inventory tracking, order processing, and other tasks, WMS can lead to increased efficiency and reduced labor costs.
One of the most promising technologies in warehouse automation is the Autonomous Case-handling Robot (ACR). ACRs are mobile robots that can autonomously move cases or trays in shelf racks. They can help warehouses increase storage density and improve picking efficiency. ACRs are gaining popularity worldwide due to their flexibility, fast deployment, and high pick rate with huge SKUs. ACRs are used in goods-to-person automation models in warehouses, where they provide a shuttle-type retrieval function to handle totes from static shelves.
In conclusion, the implementation of warehouse automation technologies will provide significant benefits to your organization. By automating inventory movement, storage, and retrieval, one can increase efficiency, reduce labor costs, and improve customer satisfaction. The recommended technologies are proven to be effective and are gaining popularity worldwide. They also offer solutions that can work with operators or in a fully automated warehouse, allowing for flexibility and phased implementations of automation. We recommend implementing these technologies in a phased approach over a period of 18 months to minimize disruption to our operations and maximize the benefits.
Checklist
While it is true that automation can benefit businesses of all sizes, there is no one-size-fits-all solution. Every operation is different, and the potential of automation varies depending on the specific needs of the business. For this reason, we propose the following checklist to identify the viability of automation for your business:
Identify the process: Identify the business process that you want to automate.
Evaluate the process: Evaluate the process to determine if it is repetitive, time-consuming, and error prone.
Determine the benefits: Determine the benefits of automating the process, such as increased efficiency, reduced costs, and improved accuracy.
Assess the feasibility: Assess the feasibility of automating the process by considering factors such as the complexity of the process, the availability of technology, and the cost of implementation.
Develop a plan: Develop a plan for implementing the automation, including the selection of the appropriate technology and the training of employees.
Implement the automation: Implement the automation according to the plan.
Monitor and evaluate: Monitor and evaluate the automation to ensure that it is achieving the desired results.
Establish can assist you in identifying the viability of automation for your business and help you develop a plan for implementation.
Budget
The cost of implementing warehouse automation technologies can vary widely depending on the complexity and scale of the automation solutions chosen. Here are some factors that can influence the budget:
Initial investment: This encompasses costs for acquiring and installing automation equipment. These expenses can vary widely depending on the complexity and scale of the automation solutions chosen.
Operational efficiencies: Evaluating how automation will reduce ongoing operational costs is critical. This includes labor savings, increased throughput, storage capacity, and scalability for peak volume, to name a few.
Total cost of ownership (TCO): Future-proofing your investment means accounting for regular maintenance and potential upgrades of the automation systems, ensuring they remain effective and efficient over time.
Return on investment (ROI) analysis: Undertaking a detailed ROI analysis is essential. This step helps in quantifying the long-term financial benefits and justifying the investment in automation.
Establish can assist you in identifying the scope and budget of automation for your business and will keep the above financial indicators in mind when proposing potential projects and implementations.
Examples
While there is an abundance of use cases and considerable number of providers within each technology introduced, here is a list of some recent automation integration projects:
DHL has deployed up to 2,000 AMRs to reduce nonproductive walking time in their warehouses.
Amazon uses AGVs to transport shelves of goods to human workers, who then pick and pack the items for shipping.
Swisslog’s AS/RS system helped a leading pharmaceutical company increase their storage capacity by 50%. DHL also uses an AS/RS system to store and retrieve items in its warehouse.
A WMS helped a leading retailer increase their order fulfillment rate by 200% and can help businesses eliminate labor-intensive duties and improve operations.
A big retail client uses automated picking systems to fulfill online grocery orders.
Warehouse Optimization: Maximizing Space Utilization and Reducing Costs
In the world of supply chain management, warehouses play a crucial role in storing and distributing goods efficiently. However, many companies struggle with limited space and rising operational costs, which can hinder productivity and profitability. The key to overcoming these challenges lies in warehouse optimization. By maximizing space utilization and reducing costs, businesses can unlock significant benefits and gain a competitive edge in the market. In this post, we will explore practical strategies and actionable tips to optimize your warehouse operations and get the most out of your warehouse or distribution center.
In the world of supply chain management, warehouses play a crucial role in storing and distributing goods efficiently. However, many companies struggle with limited space and rising operational costs, which can hinder productivity and profitability. The key to overcoming these challenges lies in warehouse optimization. By maximizing space utilization and reducing costs, businesses can unlock significant benefits and gain a competitive edge in the market. In this post, we will explore practical strategies and actionable tips to optimize your warehouse operations and get the most out of your warehouse or distribution center.
Conduct a Comprehensive Warehouse Layout Analysis: A crucial step in warehouse optimization is analyzing the current layout to identify inefficiencies and areas for improvement. Consider factors such as storage density, product flow, accessibility, and safety. By critically evaluating your warehouse's layout, you can identify opportunities to reorganize storage areas, implement better aisle configurations, and utilize vertical space effectively.
Embrace Technology and Automation: Incorporating technology and automation solutions can revolutionize your warehouse operations. Implementing the right Warehouse Management System (WMS) can streamline inventory control, order fulfillment, improve overall accuracy, and enable further improvements. Additionally, technologies like barcode scanning, RFID tagging, and automated systems can enhance picking and packing processes, reducing human errors, and saving valuable time.
Prioritize Inventory Management and Sales and Operations Planning (S&OP): It is very important to look at supply chain planning from a holistic, end to end, point of view. This will help the overall business on a strategic level and positively impact the warehouse operation by having better inventory management. Successful S&OP and inventory management is crucial for space optimization and cost reduction. By understanding your inventory levels, turnover rates, and demand patterns strategies can be implemented that minimize excess stock, reduce carrying costs, and maximize available space. Furthermore, adopting an ABC analysis methodology can help prioritize items based on their value and optimize storage allocation accordingly.
Implement Lean Principles: Applying Lean principles to warehouse operations can lead to significant improvements in space utilization and cost reduction. Techniques such as 5S (Sort, Set in Order, Shine, Standardize, Sustain) can improve the efficiency at workstations by eliminating waste and creating an organized and efficient workspace. Lean methodologies also promote employee involvement, creating a culture of continuous improvement.
Optimize Slotting and Picking Strategies: Effective slotting and picking strategies can minimize travel time, reduce labor costs, and enhance overall warehouse productivity. Analyze your SKU velocity and order patterns to strategically place fast-moving items closer to shipping areas, reducing the time taken to pick and pack high-demand products. Regularly review and adjust your slotting strategies to align with changing demand and business requirements.
Foster Collaboration with Suppliers: Collaborating closely with suppliers can help optimize warehouse operations and reduce costs. Explore vendor-managed inventory (VMI) programs which allow suppliers to monitor and replenish stock levels directly. This reduces lead times, minimizes stockouts, and frees up your warehouse space. Additionally, explore opportunities to change that way that vendors ship product to help expedite the receiving and put away processes. Potential changes include packaging, labels, and cross-docking practices to reduce handling.
Warehouse optimization is a critical aspect of supply chain management that can yield significant benefits for businesses. By maximizing space utilization, implementing efficient processes, and leveraging technology, companies can reduce costs, improve productivity, and enhance customer satisfaction. Remember, optimizing your warehouse is an ongoing process that requires continuous monitoring, analysis, and adaptation to evolving market dynamics. By adopting the strategies discussed in this blog post, you can take a proactive approach towards warehouse optimization, unlocking its full potential and positioning your business for success in the competitive market landscape.
Warehouse Scanning Technology: Additional Options to Elevate Your Warehouse Operation
Warehouse operations are continuously evolving to meet the growing demands for efficiency, accuracy, and speed in order fulfillment. While handheld RF scanners have been a staple in warehouse environments for data capture, advancements in technology have introduced alternatives that offer enhanced capabilities and improved productivity. In this post, we will explore alternatives that are redefining warehouse operations, surpassing the limitations of handheld RF scanners and opening doors to new levels of efficiency and automation.
Warehouse operations are continuously evolving to meet the growing demands for efficiency, accuracy, and speed in order fulfillment. While handheld RF scanners have been a staple in warehouse environments for data capture, advancements in technology have introduced alternatives that offer enhanced capabilities and improved productivity. In this post, we will explore alternatives that are redefining warehouse operations, surpassing the limitations of handheld RF scanners and opening doors to new levels of efficiency and automation.
Wearable Technology - Empowering Hands-Free Productivity: Wearable technology, such as ring scanners or wrist-mounted devices, is emerging as a popular alternative to handheld RF scanners. These compact devices provide hands-free scanning capabilities, allowing warehouse personnel to move freely while scanning items. With wearable scanners, workers have improved agility, enabling them to perform tasks quickly and efficiently. The convenience and ease-of-use of wearable technology streamline order picking processes, resulting in enhanced productivity and reduced fatigue.
Voice Picking Systems - Harnessing the Power of Voice Recognition: Voice picking systems leverage voice recognition technology to guide warehouse personnel through picking activities. Workers wear a headset and receive verbal instructions on which items to pick and where to find them. By responding with voice commands, workers confirm their actions, eliminating the need for manual data entry or scanning. Voice picking systems improve accuracy, enhance worker safety, and eliminate the need for handheld devices altogether. This technology allows for seamless integration with warehouse management systems, further optimizing operational efficiency.
Mobile Computers - The Power of Data and Functionality in One Device: Mobile computers, also known as rugged tablets or handheld computers, offer a versatile solution for warehouse operations. These devices combine the functionality of a scanner and a portable computer in a single device. Equipped with built-in barcode scanners or capable of connecting to external scanners, mobile computers provide a larger screen for displaying information and enable real-time communication with warehouse management systems. They offer additional functionalities beyond scanning, such as inventory management or order tracking, empowering workers with comprehensive data and tools at their fingertips.
Vision Systems - Advancements in Visual Recognition Technology: Vision systems leverage cameras and image recognition technology to capture and process data in warehouse operations. These systems can automatically scan and decode barcodes or labels, eliminating the need for manual scanning. By integrating vision systems with conveyor belts or automated sorting processes, items can be identified and tracked accurately without human intervention. Vision systems offer rapid and reliable data capture, improving efficiency and throughput in the warehouse while reducing reliance on handheld scanners.
RFID Technology - Enabling Real-Time Inventory Visibility: RFID (Radio Frequency Identification) technology has gained prominence in warehouse operations, offering a highly efficient alternative to handheld RF scanners. RFID tags are attached to items, pallets, or containers, and RFID readers or antennas capture the data wirelessly. Unlike traditional barcode scanning, RFID technology does not require line-of-sight scanning and can read multiple items simultaneously. This enables real-time inventory visibility, automates tracking processes, and reduces manual data entry, resulting in improved accuracy and streamlined operations.
As the demand for speed, accuracy, and efficiency in warehouse operations continues to grow, alternatives to handheld RF scanners are revolutionizing the industry. Wearable technology, voice picking systems, mobile computers, vision systems, and RFID technology offer advanced capabilities that surpass the limitations of traditional handheld scanners. By leveraging these alternatives, warehouses can enhance productivity, improve worker safety, achieve real-time inventory visibility, and streamline operational processes. Embracing these advancements empowers warehouses to stay ahead of the competition, meet customer expectations, and unlock new levels of efficiency and automation in their operations.
Order Picking in the Warehouse: Choosing the Right Strategy
Order picking is one of the most important processes in a warehouse or distribution center, making up the majority of operating costs and directly impacting service levels. Selecting and implementing the right picking strategy will ensure accurate on-time deliveries and cost-effective labor. In this article, we will review some different order picking strategies and how they can improve an operation.
Order picking is one of the most important processes in a warehouse or distribution center, making up the majority of operating costs and directly impacting service levels. Selecting and implementing the right picking strategy will ensure accurate on-time deliveries and cost-effective labor. In this article, we will review some different order picking strategies and how they can improve an operation.
Single Order Picking
One of the most common picking methods is single order picking. Just as it sounds, this method requires one order to be picked at a time, from start to finish, by a single operator. This method is easy to learn, does not require advanced technology, and is less prone to errors due to its simplicity. Single order picking is best suited for smaller warehouses or where entire pallets are picked. For larger and more complex operations, single order picking becomes inefficient due to the high amount of travel required throughout the warehouse.
Batch Picking
Opposite to single order picking, batch picking groups multiple orders together that have the same SKUs, which are later sorted by an operator before being shipped. The main advantage batch picking has over single order picking is the ability to pick multiple orders in a single trip, which improves operator productivity. Due to the increased complexity of batch picking, a warehouse management system (WMS) and order management system (OMS) are required to properly route and track orders throughout the warehouse.
Cluster Picking
For cluster picking, multiple orders are picked, from start to finish, by a single operator. This method is different than batch picking in that each order is sorted as it is picked. This is accomplished with the help of a cart containing individual totes for the operator to place SKUs in as they are picked. Cluster picking does not require a warehouse management system (WMS) and works best for smaller orders and smaller warehouses. This can create significant improvement from single order picking since the operator’s total distance traveled is reduced.
Zone Picking
With zone picking, the warehouse is split into individual zones that an operator will pick from. Operators will pick all the SKUs for an order in their zone and then send it to pack or the next zone if it is incomplete. This method can be used independently or in conjunction with the above-mentioned methods. This is a valuable option for high volume warehouses that struggle with operator congestion in aisleways.
Wave Picking
Wave picking can be utilized independently or in congruence with the above-mentioned methods. Wave picking groups orders together and releases them to operators in batches or “waves”. Orders can be grouped together based on a variety of different factors, such as shipping schedules, shift changes, product characteristics, etc. Wave picking is best suited for operations that are using batch or zone picking, already have a warehouse management system (WMS) and order management system (OMS) in place, and are looking to fully optimize their picking strategy.
Choosing the right order picking strategy is a great start to optimizing a warehouse operation. The best strategy will vary based on company size, inventory size, number of orders, SKUs per order and technological capabilities. At Establish, we combine a fact-based approach with state-of-the-art technology including warehouse simulations and data analytics to determine the optimal picking strategy for organizations.
Supply Chains in 2021 and What to Expect in 2022
The year 2020 presented the world with some incredible challenges, especially in the world of supply chain. Almost two years later, the COVID-19 pandemic and supply chain issues remain a major challenge for the entire globe. Now that 2021 has come to an end, we want to look back on what happened last year and talk about what we expect to see in 2022.
The year 2020 presented the world with some incredible challenges, especially in the world of supply chain. Almost two years later, the COVID-19 pandemic and supply chain issues remain a major challenge for the entire globe. Now that 2021 has come to an end, we want to look back on what happened last year and talk about what we expect to see in 2022.
2021 Recap
There is a lot to cover when looking back at supply chain and logistics in 2021 but we want to focus on two major topics that cover many different areas.
Cost Increases
A huge theme of 2021 was the continued increases to all costs across supply chain and logistics. Within transportation, we saw parcel carriers continue to hike up rates, while LTL and Truckload rates also continued to rise. One of the main drivers to the higher rates is that the demand for shipping remains way above the current capacity that exists. Perhaps the most extreme case of this was seen within the ocean container shipping industry. The cost to ship an ocean container at the end of 2021 was 3-7 times more expensive than in 2020, depending on the route. In addition, the congestion seen at the ports is causing dwell times to escalate, resulting in more costs due to the incurred fees.
The transportation industry was not the only area within supply chain and logistics to see cost increases. We also saw 3PL prices and warehouse rates increase dramatically. Many of our clients saw 3PLs increase transactional costs by up to 30%. The cost of leasing and owning a warehouse also increased across the board, especially in areas like southern California. This reflects the demand for warehouses and 3PLs growing faster than the availability.
Throughout the year, labor shortages also became a major headline in all industries, especially in warehousing and manufacturing. To maintain a sufficient workforce, many companies were forced to increase wages, adding even more costs to the supply chain.
Investment in the Supply Chain
Many of the reasons for the cost increases discussed in the previous section were due to demand being greater than the supply. This caused people and companies to take action, as investment in the supply chain and logistics was another main theme that was seen in 2021 and that we expect to see continue going forward.
In years past, reducing supply chain costs was always the main focus for our clients during supply chain network optimization projects. This year, service level and transit time to customers was emphasized more and more, even if it meant higher costs. Two of the world’s largest companies, Walmart and Amazon are a perfect example of this. Walmart has credited some of their 2021 growth to an increased focus on their e-commerce business and omni-channel development. To increase their ability to fulfill orders quickly, Amazon opened nearly 300 facilities in 2020 and the 2021 number is expected to be large as well.
Companies are also looking at supply chain optimization as a more competitive tool, focusing on organizing supply chains globally and across all business units rather than each region/business operating independently. This will require some heavy investments up front in order to improve the business over the long term.
In addition to companies investing in their own supply chains, investment firms also have been investing in transportation and warehousing. This is a direct result of the high demand for transportation and warehousing outweighing the existing capacity. These investments should bring additional capacity to the market in the years to come.
Investments in sustainability also became a major focus in 2021, with numerous companies making pledges towards net zero emissions. Over 200 companies globally have joined The Climate Pledge, to have zero net emissions by 2040.
What to Expect in 2022
We expect many of the trends and challenges from 2021 to continue but ease a bit in 2022.
More Capacity for Freight and Warehousing
We expect to see a lot of new capacity entering the market in transportation and warehousing thanks to the investments seen in the supply chain industry in 2021. This should cause trucking rates and ocean rates to continue to plateau and eventually be reduced but rates are expected to remain elevated in 2022. We expect to see a very similar trend in the warehousing and 3PL market as the additional capacity coming onto the scene should level out the price increases and eventually cause costs to drop slightly. However, like transportation costs, we think prices will continue to be elevated.
Increased Compensation
We anticipate more companies offering better pay and benefits to compensate for the labor shortages and attract a more capable work force.
Continued Investment in the Supply Chain
With the huge demand for carriers, 3PLs and warehouse space, we expect to see continued investment in supply chain. We also expect companies to continue to focus on warehousing and building out their distribution networks to increase their service levels to their customers. Many companies, especially online retailers, saw rapid growth over the past year. This has made warehousing a top priority for a lot of companies as they are quickly outgrowing their current operations. Many companies will not be able to support their growth without optimization, automation, and expansion.
Continued Growth in 3PL Demand
With e-commerce producing so many new companies and altering the business models of existing companies, the need for warehousing space is at an all-time high. For many companies, it makes sense to outsource this to experts rather than try and build a warehouse operation internally, so we expect an even greater desire for 3PLs in 2022.
A Focus on Global Supply Chains
We expect companies to continue using fulfillment and logistics as a competitive tool; companies are going to start looking at all business units and supply chain functions together to leverage any opportunities to integrate, optimize and reduce costs. We also anticipate the growth of nearshoring and more local and diverse sourcing to continue. This become a topic of conversation in 2020 and we started to see this come into action in 2021 but restructuring of this size takes a long time so results will not be seen until we get a bit further down the road.
A Continued Shift Towards Sustainability
We also expect to see a continued focus on sustainability in 2022 and beyond as restructuring supply chains can have a massive impact on a company’s greenhouse gas emissions.
We at Establish wish everyone a safe and healthy 2022!