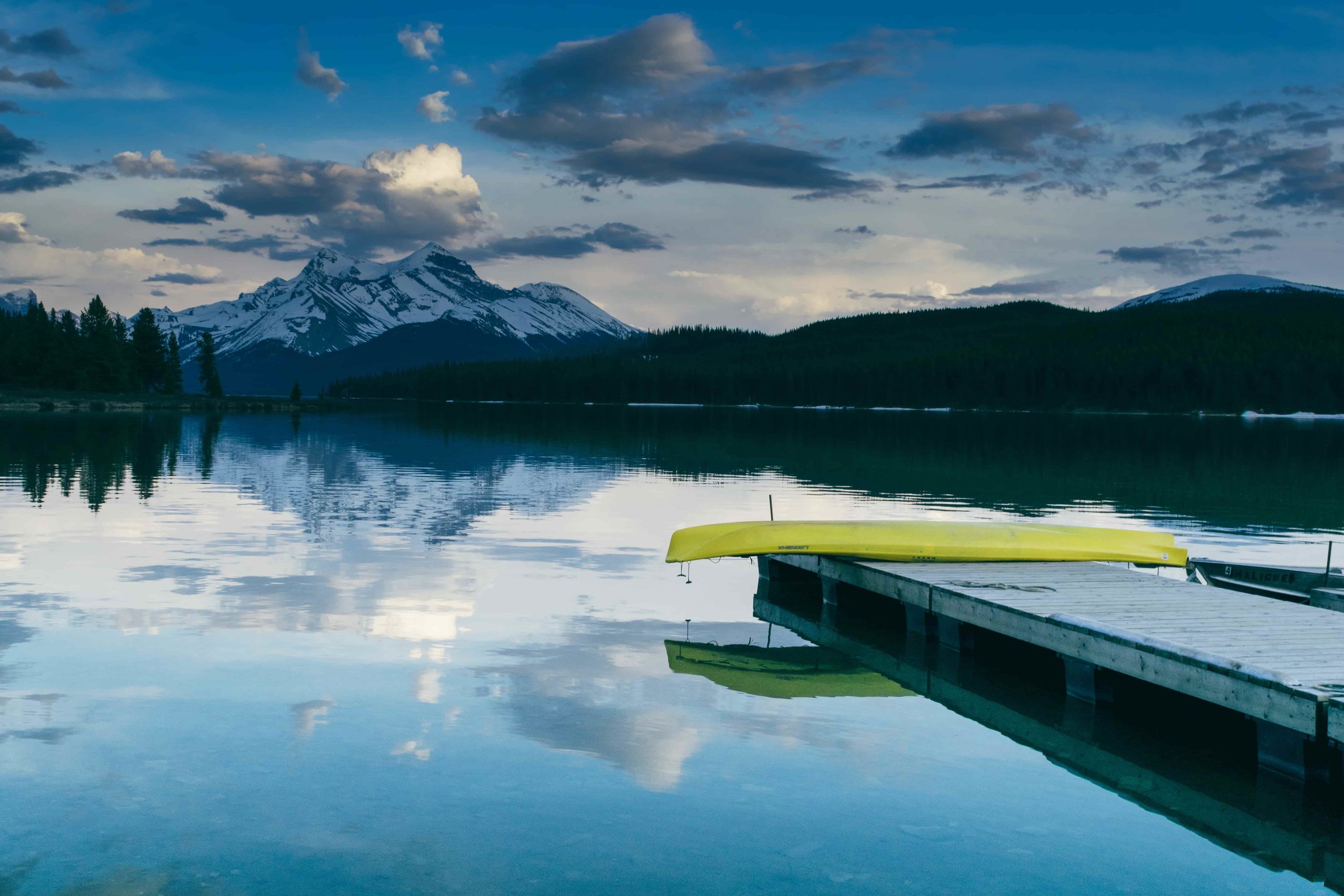
THE SUPPLY CHAIN BLOG
The Warehouse Rack Layout Aisle Width Decision
As warehouse consultants, we are fortunate to visit and improve hundreds of distribution operations. The majority, but not all, of the operations require forklifts of some sort. Upon starting my career, one of the things I expected to see in the operations was more standardization of forklift types and, by extension, aisle width. However, that is not the case.
As warehouse consultants, we are fortunate to visit and improve hundreds of distribution operations. The majority, but not all, of the operations require forklifts of some sort. Upon starting my career, one of the things I expected to see in the operations was more standardization of forklift types and, by extension, aisle width. However, that is not the case. Operations of similar applications and volumes can often have different forklifts and aisle widths. Here, I’ll explore some reasons why this may be:
Facility – Oftentimes, the facility may be the constraint. When creating pallet rack layouts, column lines cannot be in the aisles and are best buried in the flue spaces. As such, sometimes the column grid guides the aisle width decision. Also, the facility could have limited height, encouraging bulk floor storage where possible, which limits the truck types used.
Warehouse Management System (WMS) – Some types of racking, such as double deep, drive-in or pushback, require additional functionality to the WMS. Without the functionality, many types of rack cannot be used optimally, which affects the truck type and aisle spacing.
Item Profile – If an item is heavy or bulky, it may require a certain type of truck (for example, a counterbalance instead of a reach) or an extra-long aisle for maneuverability. The reverse is true if an item is too small and only fits in shelving.
Inventory Profile – If the inventory profile contains many pallets of few SKUs as opposed to many SKUs of few pallets, it affects the optimal racking method, thus affecting aisle width and truck decision.
Order Profile – If items are picked in full pallets as opposed to each or case quantities, the best picking method will then drive the truck and rack selection.
Though two operations may appear similar, there are many factors that go into selecting the right aisle width and forklift type. It is not a one size fits all solution nor an easy decision - it requires analysis of several variables.
Canadian Distribution Strategy for U.S. Organizations
For many American companies, Canada can be an afterthought considering its small size relative to the US. However, given its intricacies, it would be a mistake for American companies to assume that Canada is much the same as the US as the Canadian market and topography is very different from that of the United States. The key to unlocking the best Canadian distribution strategy is to understand these differences.
For many American companies, Canada can be an afterthought considering its small size relative to the US. However, given its intricacies, it would be a mistake for American companies to assume that Canada is much the same as the US as the Canadian market and topography is very different from that of the United States. The key to unlocking the best Canadian distribution strategy is to understand these differences.
Canada’s population is 11 percent of the U.S. population based on 2015 data, despite being nearly 25% larger than the contiguous lower 48 United States (38.85 MM square miles vs. 31.12 MM square miles). The Canadian population is primarily inhabited near the continental U.S. border which is 3,987 miles long, as the population map below shows:
Map created in Tableau. Data source: http://www12.statcan.gc.ca/census-recensement/2011/dp-pd/hlt-fst/pd-pl/Table-Tableau.cfm?T=301&S=3&O=D
The distribution to Canadian customers can be complex as a result of market, distance, regulations and tax requirements. However, many companies have evaluated their options and selected one of the following distribution strategies either shipping direct from U.S. or establishing warehousing operation(s) in Canada. The selection of which distribution is right depends on a number of factors, such as:
Sales volume
Service requirements
Distribution center costs
Transportation costs
Inventory carrying costs
Type of customer
Etc.
Here are some high-level benefits/disadvantages depending on the strategy:
4 Reasons to Consider Outsourcing Distribution to a 3PL
In today’s on-demand economy, there is a growing number of customers ordering online and who want their products as soon as possible. When you compare this to the past, when consumers did all of their business in-person, it’s quite the contrast. From a warehousing and distribution perspective, it might as well be night and day.
In today’s on-demand economy, there is a growing number of customers ordering online and who want their products as soon as possible. When you compare this to the past, when consumers did all of their business in-person, it’s quite the contrast. From a warehousing and distribution perspective, it might as well be night and day. Gone are the days of full pallets being sent to retailers or regional DCs and here to stay are the days of breaking cases to ship eaches. This monumental change in warehousing is one of the reasons why many companies are outsourcing distribution to Third Party Logistics Providers (3PL). Is outsourcing distribution to a 3PL the right move for you? Below are 4 reasons why it could be.
1. Changing Supply Chain
As mentioned above, the nature of fulfillment has changed and will keep changing. If your company is set in its ways of not shipping to consumer and is looking to expand to e-commerce, a 3PL could be a viable option. Various 3PLs specialize in e-comm and have set-ups ready-made to absorb your business, as well as potential in obtaining favorable parcel rates. It may be a better move to outsource this new mode of fulfillment than to attempt it yourself, especially if there is no in-house experience.
2. Lack of In-House Knowledge
If your company does not have in-house expertise in distribution, a 3PL could be a good move for a couple of reasons: first, the 3PL may be able to reduce costs. Distribution is their business and expertise, so, depending on your levels of efficiency, they can run it more efficiently. Secondly, if you don’t have the in-house knowledge, your day-to-day may be stressful – outsourcing reduces those headaches.
3. Business Changes
A different reason to outsource is a change in business forecast. If your company is rapidly growing, making acquisitions or combining subsidiaries, for example, there are a lot of changes coming to your supply chain. Your warehousing needs can vary in large swings year over year, making an owned or leased building an inefficient option for your distribution operation. The best option would be a 3PL shared warehouse where the 3PL can absorb business changes in their idle space and the infrastructure is already in place to avoid the inefficient and expensive warehouse transitions.
4. Market Expansion/Service Level Improvement
Say you are a company with one DC in the Midwestern United States. Your East Coast customers love your quick lead times, but your Western customers are starting to get a little irked about how they can only get a shipment a week after you process it. How can you make them happier without committing to the long-term? A second DC on the West Coast with a 3PL. This way, you can evaluate the benefits and costs of a second operation without committing to long-term infrastructure investments. A similar reason is to expand into a new market: the best bet for an international company with no US presence is to use a 3PL for much of the same benefit.
These are just some reasons to consider a 3PL – every company has a unique situation and evaluation to make. Need help evaluating if a 3PL is right for you? Establish has completed hundreds of 3PL evaluations and searches and have worked with nearly every 3PL in North America. Give us a call at 212-776-9900 or e-mail us at info@establishinc.com to discuss your supply chain needs.
Consolidating Parts to One Centralized MRO Storeroom
A modified wood products manufacturer was planning construction of an additional plant to fulfill increasing demand. The company had already developed a preliminary layout of the facility in tandem with an architect for budgetary purposes. Establish was tasked with maximizing the storage capacity of the Maintenance, Repairs and Operations (MRO) storeroom space allocated in the preliminary layout.
The Challenge
A modified wood products manufacturer was planning construction of an additional plant to fulfill increasing demand. The company had already developed a preliminary layout of the facility in tandem with an architect for budgetary purposes. Establish was tasked with maximizing the storage capacity of the Maintenance, Repairs and Operations (MRO) storeroom space allocated in the preliminary layout.
Developing a Cost-Efficient MRO Storeroom
All parts at the existing facility were stored at the point of use. While this provided quick turnaround time in the event of a line breakdown, there were several disadvantages to point of use storage:
Securing inventory was nearly impossible. Outside of the primary storeroom, inventory utilization was retrieved by the user and not updated in inventory until control retrieved the use sheets from the location.
Inventory management took an extremely long time to execute. Inventory control had to walk several miles in order to cover the fourteen locations.
The same item was stored in multiple locations. Each location stored extra, thereby increasing the total part inventory.
In order to be close to its point of use, some items were stored in less than ideal locations.
As a result of these flaws, the hypothesis was that the MRO inventory should be centralized in one location, with some of the items only utilized in one location stored at point of use.
Similar to other MRO warehouses, there is wide range in item usage frequency. Some items are accessed several times a day whereas other items aren’t accessed for years. Unlike a typical warehouse, the items that haven’t been used in years are not necessarily obsolete, as these parts may be hard to find, not manufactured any more, or the part may be essential to run the production line. As a result, Establish explored and ultimately recommended customized solutions to match item utilization. Frequently used items were located in the front of the storeroom and are located on shelves for easy picking. Items rarely used were stored on space efficient narrow aisle pallet racks, accessible only by pallet walkers.
Results
The lumber company got a highly efficient layout that consolidated the storage requirements of the fourteen locations in the existing facility into the one space provided in the proposed facility. Only 60% of the anticipated footprint was needed and the inventory control improved.
Key Takeaways
There are tradeoffs between storing items at its point of use and at a centralized location. The conclusion is however that the savings in space, inventory and handling far outweighs the easy access. Most important is the inventory control that ensures that the right items are available.
Item usage frequency is important when determining item storage capacity. The less an item is retrieved, the more inconvenient a location it can be stored in. This inconvenience can be purely positional, such as storing the item in the back of the warehouse, or be due to increased storage density, such as utilizing compression shelving to increase storage capacity in the same footprint.
Warehouse Design for a Greenfield Building Material Plant
A modified wood products manufacturer was planning construction of an additional plant to fulfill increasing demand. The company had already developed a preliminary layout of the facility in tandem with an architect for budgetary purposes.
How Can We Reduce The Warehouse Footprint?
A modified wood products manufacturer was planning construction of an additional plant to fulfill increasing demand. The company had already developed a preliminary layout of the facility in tandem with an architect for budgetary purposes.
A team of warehousing experts from Establish was tasked with reviewing the finished goods warehouse layout in tandem with the architect to reduce the warehouse footprint and resulting construction costs while identifying optimal process flows, storage capacities and item slotting in the proposed layout.
Developing a Cost-Efficient Warehouse Design
We began by observing the operations at an existing plant to identify the handling and storage processes from manufacturing to shipping. There were many similarities that could be incorporated in the proposed facility; however, the joint evaluation revealed three key differences:
The proposed facility will produce fewer SKUs than the existing facility.
The proposed facility will ship finished goods exclusively by flatbed truck whereas the existing facility shipped via a mix of truck and railcar.
The proposed facility can rely on two close-by facilities to store additional finished goods inventory, minimizing any potential impact of inefficiencies resulting from an overloaded warehouse.
The client adjusted the mix on the expected production capacity, giving Establish the foundation to develop a layout to store the anticipated finished goods capacity. As items ranged between eight to ten feet in length based on SKU, adequate item slotting for each item size was maintained throughout the design process.
Establish modeled the shift in outbound volumes and developed potential second step layouts for both railcar and flatbed truck loading areas to accommodate these volumes.
The client also identified a two week time period when the production line shut down. This resulted in significantly larger inventory storage requirements than during the balance of the year. To address this, Establish developed a layout and process to temporarily store during this surge of inventory while minimizing impact on warehouse functionality.
Results
The modified warehouse layout significantly reduced the size of the proposed footprint while still developing a highly efficient warehouse layout. As a result, the company was able to reduce the budgetary cost of the warehouse section of the facility by over $2 million.
Key Takeaways
In a warehouse with varying item sizes, it is very important to incorporate item slotting early in the process. Adequate storage capacity should be accommodated for each item size and not simply overall. Averages often lie.
Accommodating short periods of inventory surges can be incorporated into layouts without utilizing temporary offsite storage. However, less efficient handling must be accounted for during the inventory surge.
Identifying outbound volumes by mode is important in determining outbound staging requirements, which is a main driver of space requirements. In this case, loading into railcars is significantly different than loading flatbed trailers (in both space required for forklift movement and carrying capabilities). This also applies to parcel shipments, as additional space for packaging is required and order sizes are much smaller.
When to Outsource Warehousing, and When to Keep It In-House
The sizing of your warehouses is likely to always be wrong and risk being in the wrong geographical location if you want to integrate your acquisitions into your infrastructure. A flexible outsourcing contract will be easier to adapt to accommodate your ever changing new realities.
Outsource
If your strategy is to grow through acquisitions
The sizing of your warehouses is likely to always be wrong and risk being in the wrong geographical location if you want to integrate your acquisitions into your infrastructure. A flexible outsourcing contract will be easier to adapt to accommodate your ever changing new realities.
If you (or someone else) want to minimize capital expenditures
There will be no burden on your balance sheet with an operation outsourced to a 3PL. It will also ensure that you have the latest software and appropriate equipment without having to go through the labor intensive investment application processes.
If you’re having short peaks in capacity demands
Obviously you don’t want to build and pay for capacity that is only used for a limited period or infrequently Two big issues though; First, you would probably want to do a storage only solution since it costs too much time and effort to set up in the WMS system. This brings us to problem number two, which is that you are probably not the most attractive customer for any 3PL, so it can be hard to find a good one.
If you need to get the logistics together quickly and don’t have the resources
We would, of course, argue that it is a good idea to hire good logistics consultants to sort out your problems. However, if there isn’t anyone to catch the ball and run with it, then it’s better to face reality and let a good 3PL run your warehouse operations.
When you don’t have the size to get the economy of scale
If your volumes are small it could be hard to defend investments in WMS systems, up-to-date-equipment and the resources to manage it.
When your volumes are shrinking
When you are in a revenue decline you want to have your costs as variable as possible. Outsourcing your logistics is a very good card to play.
Keep Warehousing In-House
If money matters
Many 3PLs run efficient and high quality warehouse operations. It is very rare to come across not-for-profit 3PLs so typically you pay for the services. Also, you will likely find that there are costs you never expected that will bring the margin up. So, if you have a good team and you know what you are doing, chances are very good you will save money by operating the warehouse in-house.
If you perform a lot of value added services in the warehouse
In general, it is easier to get good prices on standard services such as receive a pallet, store it for a month and then pick it and ship it. For special services the margin is often higher as is the cost to train someone to perform the task.
If logistics services is an important part of your offerings or your cost mass
When logistics really matter and your company is stable, you are better off figuring out how to run a good warehouse operation on your own. Then you are in control, and can develop better solutions since you have the knowledge and the skills to see what would work best for you.
Seven Trends in Logistics
Warehousing; In-House or Outsourced? On one side, the 3PL providers are getting better and have all the credentials needed, which is tearing down a lot of the walls of resistance towards outsourcing. On the other side is the feeling of lost control and freedom that could be needed as logistics is getting even more important. There are a lot of other reasons, but everybody is talking about it.
1. Warehousing; In-House or Outsourced?
On one side, the 3PL providers are getting better and have all the credentials needed, which is tearing down a lot of the walls of resistance towards outsourcing. On the other side is the feeling of lost control and freedom that could be needed as logistics is getting even more important. There are a lot of other reasons, but everybody is talking about it.
2. Ocean Freight
At CSMCP this was the topic for of many discussions and it is changing the thinking in many companies. The intensive rate hikes the last year and the unreliable capacity are some of the problems to wrestle with. It is also a part of the background to the on-shoring, even though it is more anecdotal than substantial statistical facts this far. On-shoring will make the list soon.
3. White Glove Services
The term used to refer to companies carrying the furniture into the living room. Now it is often used to refer to the value added services in conjunction with the delivery of a physical product. This service is getting more integrated in the physical product and treated more as a source of revenue than a nuisance. The final yards of the delivery is getting more important as the only physical contact with the customer for many companies.
4. S-a-a-S
The Software-as-a-Service concept has enabled smaller companies to operate good and modern WMS and TMS, which facilitates a smaller revolution when it comes to efficiency.
5. Intermodal Traffic
It has been talked about for a while and now nobody wants to miss the train (!) The increase in domestic container shipments on rail increased by 7% in the third quarter of 2014 over the same quarter in 2013 according IANA.
6. Fuel Prices
The gas price has decreased by 78 cents per gallon from May 2014 to November 2014. What will this mean for the trucking industry? Will the carriers change the fuel surcharge formulas?
7. Distribution Structures
Partly connected to the number 1 on the list. With the economy taking off and volumes increasing, we see a lot of companies reevaluating their distribution networks. The managements have learned that there are big savings to be had by optimizing the distribution networks and don’t want to miss out.
Warehouse Design in the Real World
Hakan Andersson discusses warehouse design in the real world.
Hakan Andersson discusses warehouse design in the real world. The main takeaways for getting a very efficient and low investment warehouse design for high-volume goods with few SKUs:
Separate flows, inbound flows from outbound flows.
Automate where the flows are big enough.
Abundance of dock doors to enable live loading into drop trailers.
When you have high enough volumes, don’t be shy from using the floor stacking.
Project Background
Just a short background. This company is a food company; they produce consumer food for retail. It’s high-volume goods and, relatively speaking, few SKUs. We have one or two hundred SKUs we’re handling here.
The Challenge
The challenge in this project was they just acquired a new brand, so they wanted to host double the production volumes; the facility should host that. We would like to do this, and this is then the outcome as well, because we succeeded in having very low investments. It turned out that we could handle double the production volumes with just marginally expanded workforce when it comes to material handling.
Then, as is for most companies, there was an urge to have this be very flexible.
Lessons Learned
1. Separate inbound flows from outbound flows
The first major lesson here was when we did all the analysis and we tried out a lot of different scenarios.
What made a huge impact was to separate the flows, inbound from outbound. With the original layout, there was plenty of dock doors but they were all at the same place. In this instance we made a design where we opened up doors that were coming in directly to the production line.
The reason we did that is we wanted to minimize the crossing traffic. When you have that high volumes as we have in this case, when you have a production, you have all the packaging material, the driving distance quickly adds up to be very much.
2. Automate where the flows are big enough
The second takeaway here was that when the volumes are high enough, it makes sense to automate. In this case this is true for the inbound material, packaging material.
We have very high, repetitive flows. We put dock doors close to where you feed the production lines.
With packaging material, we put drop trailers and used them as storage. The ingredients would come in through pipelines, so we didn’t have to handle that at all; pipelines and conveyors. By having the drop trailers with the packaging material, we could then unload them directly from the trailers. One touch on to gravitating conveyor belts that were feeding the packaging machines.
This took away a lot of handling, and it also helped a lot with disconnecting the feeding of the production line from material handling. Then we had a robot that was emptying the totes in the production lot.
3. Abundance of dock doors to enable live loading into drop trailers
The third takeaway here was that it made a lot of sense to install an abundance of dock doors. This way we could enable live loading of the drop trailers—again, one touch—and we would also reduce the need for staging space, which is very space-consuming in normal warehouse design and a very critical part of it too.
And we then set up routines to direct the trailers to the doors that were nearest to where the majority of the products were stored. This made a huge difference when it came to the staffing requirements.
4. Use floor stacking when volumes are high enough
The fourth major takeaway here is regarding storage equipment. In this case, as always I would say, the 80/20 rule is very applicable, which meant that we had a lot of products with less than five pallets an average storage volume. For them, we set up pallet racking, but that would leave us, then, with very few SKUs.
We started out with, say, 150 to say that we had 25 to 30 SKUs that were produced in very high volumes.
For those, it made a lot of sense to floor stack them; we would floor stack them two high and nine deep. No investment at all and racking for them, very space-efficient; just so deep, you could stack them too high that without the aisles that you would have with a racking solution, it’s actually surprisingly space-efficient, and it’s a very flexible solution.
It also means that you have a built-in ability to expand in increments by putting in four deep, four high driving racks.
Summary
The main takeaways here that are making it very efficient and low investment for high-volume goods with few SKUs:
Separate flows, inbound flows from outbound flows.
Automate where the flows are big enough.
Abundance of dock doors to enable live loading into drop trailers.
When you have high enough volumes, don’t be shy from using the floor stacking.